How To Choose Drive Rollers For Rolling Groove Machine
Discussion On Drive Roller Size Design
Our RG-5X Drive Roller |
||||
size: | 1"-1 ½" |
2"-3" |
3 ½"-6" |
8"-12" |
PK
Other sellers Drive Roller |
|||
size: |
1"-1 ½" |
2"-6" |
8"-12" |
Discussion on the configuration design of the Drive Roller of the RG-5X steel pipe rolling groove machine
In the design of the RG-5X steel pipe rolling machine, we specially selected the Drive Roller configuration of 1"-1 1/2"; 2"-3"; 3 ½"-6"; 8"-12". Rather than a larger range of Drive Roller configurations such as 1"-1 ½", 2"-6", 8"-12". There are many considerations behind this design decision, mainly focusing on rolling groove speed, efficiency, pressure wheel diameter and pipe diameter adaptation, etc.
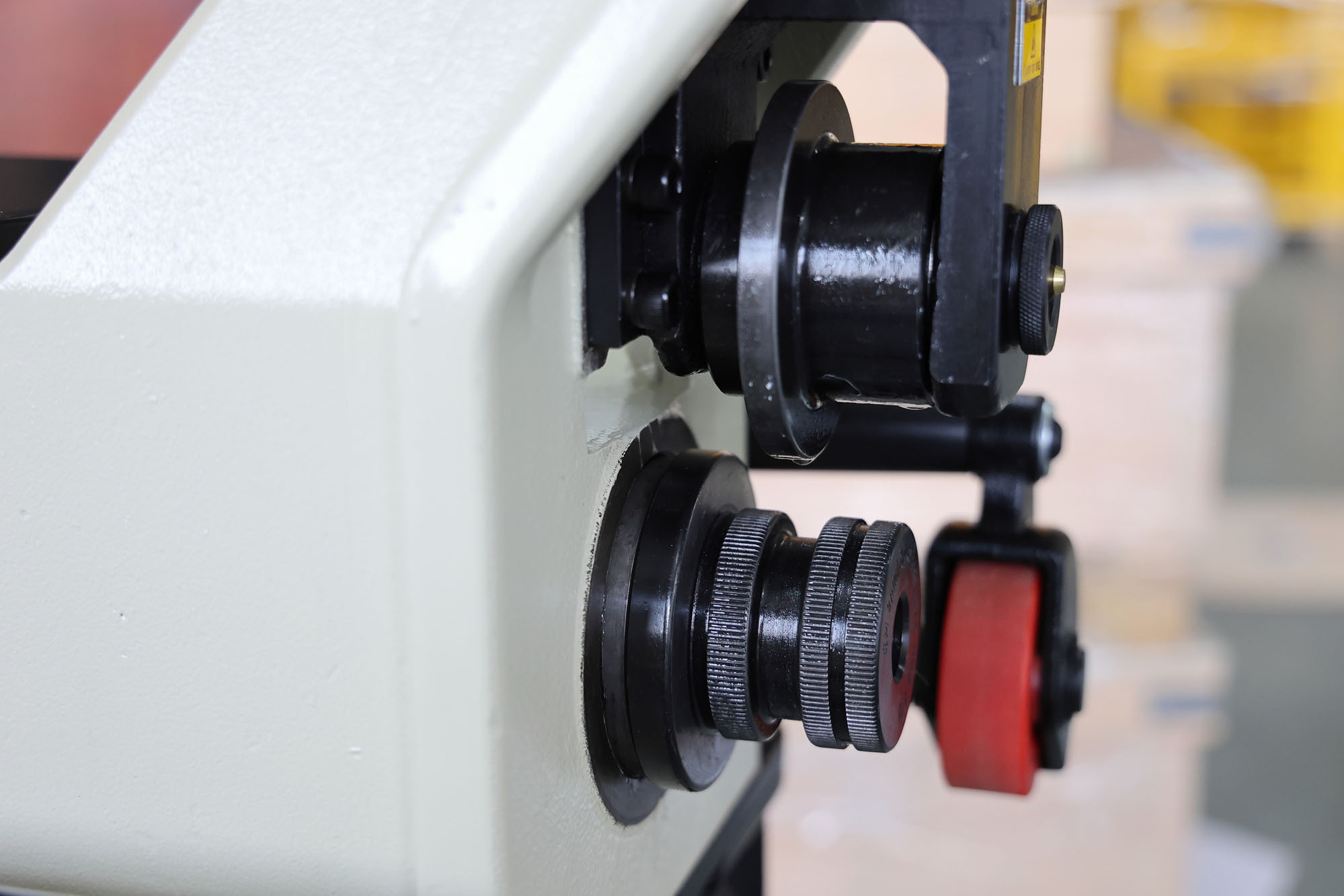
Considerations of rolling groove speed and efficiency
Using a single set of drive rollers to cover the pipe diameter range of 2"-6" may appear to reduce the frequency of replacement of drive rollers, but in actual operation, especially for roll grooving operations with pipe diameters of 4"-6", There will be a problem of significant speed reduction. This is because the diameter of the drive roller is small and the rotation speed of the rolling groover/products-list.htm is constant. When a small-diameter drive roller is used to roll a large-diameter pipe, the effective workload per unit time is reduced, resulting in a significant decrease in efficiency.
More importantly, when the small-diameter drive roller rolls the groove on the large-diameter pipe, the pressure applied is not uniform enough, and the bell mouth that is easily pressed out is relatively large. This not only affects the quality of the roll groove, but may also result in reduced accuracy and consistency of the finished product.
If you frequently need to groove 4"-6" pipes, our RG-5X grooving machine is your best choice.
Adaptation of groove roller and drive roller diameters
A common question raised by many customers is whether a 2"-3" drive roller should be larger than a 2"-6" one. This actually involves the different functions and design logic of the drive roller and groove roller.
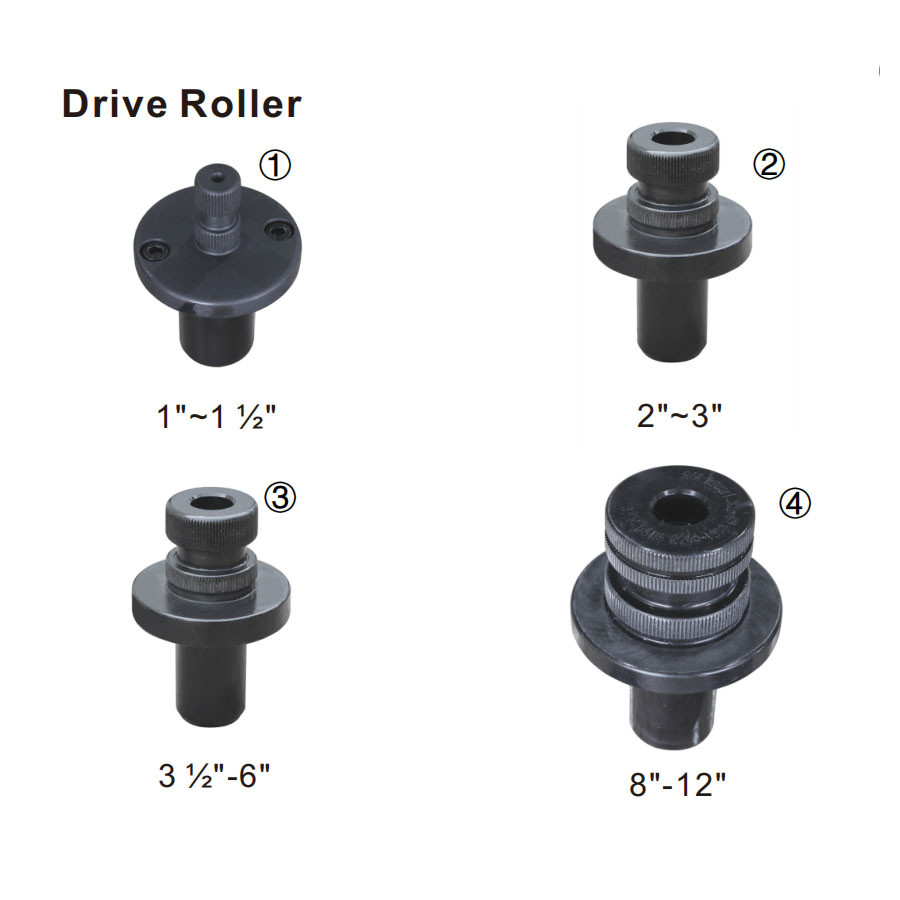

The diameter of the drive roller is designed to be small to accommodate the delicate operation of small-diameter pipes. The 2"-3" drive roller has a smaller diameter precisely to match the 2"-3" pipe diameter to ensure the accuracy and uniformity of the rolling groove operation. During the rolling grooving process, the pressure wheel rotates passively, and its main function is to support and guide the pipe into the position of the drive roller. Therefore, the rolling groove speed is mainly determined by the diameter of the drive roller, not the pressure roller.
In reality, a 2"-3" drive roller and a 3 ½"-6" drive roller are different in size and function, although they may look similar. The former is specifically designed for smaller diameter pipes, while the latter is optimized for larger diameter pipes. Using smaller drive rollers to perform rolling grooving operations on large pipe diameters is not only inefficient, but also causes unnecessary wear and tear on equipment and pipes.
Reasonable configuration of drive roller
The drive roller is configured in sections, such as 1"-1 1/2"; 2"-3"; 3 ½"-6"; 8"-12", which can ensure optimal operation within the diameter range of each section. This configuration not only improves processing efficiency and reduces the number of replacements of the dirve roller, but also provides the best rolling groove quality and accuracy within different pipe diameter ranges.
In actual operation, although in theory it is possible to roll 4"-6" pipes using a 2"-3" drive roller, doing so will significantly reduce the operating efficiency and increase the rolling time. Therefore, configuring different drive roller groups for different pipe diameter ranges is to ensure that the best performance and effects can be achieved in each operating range.
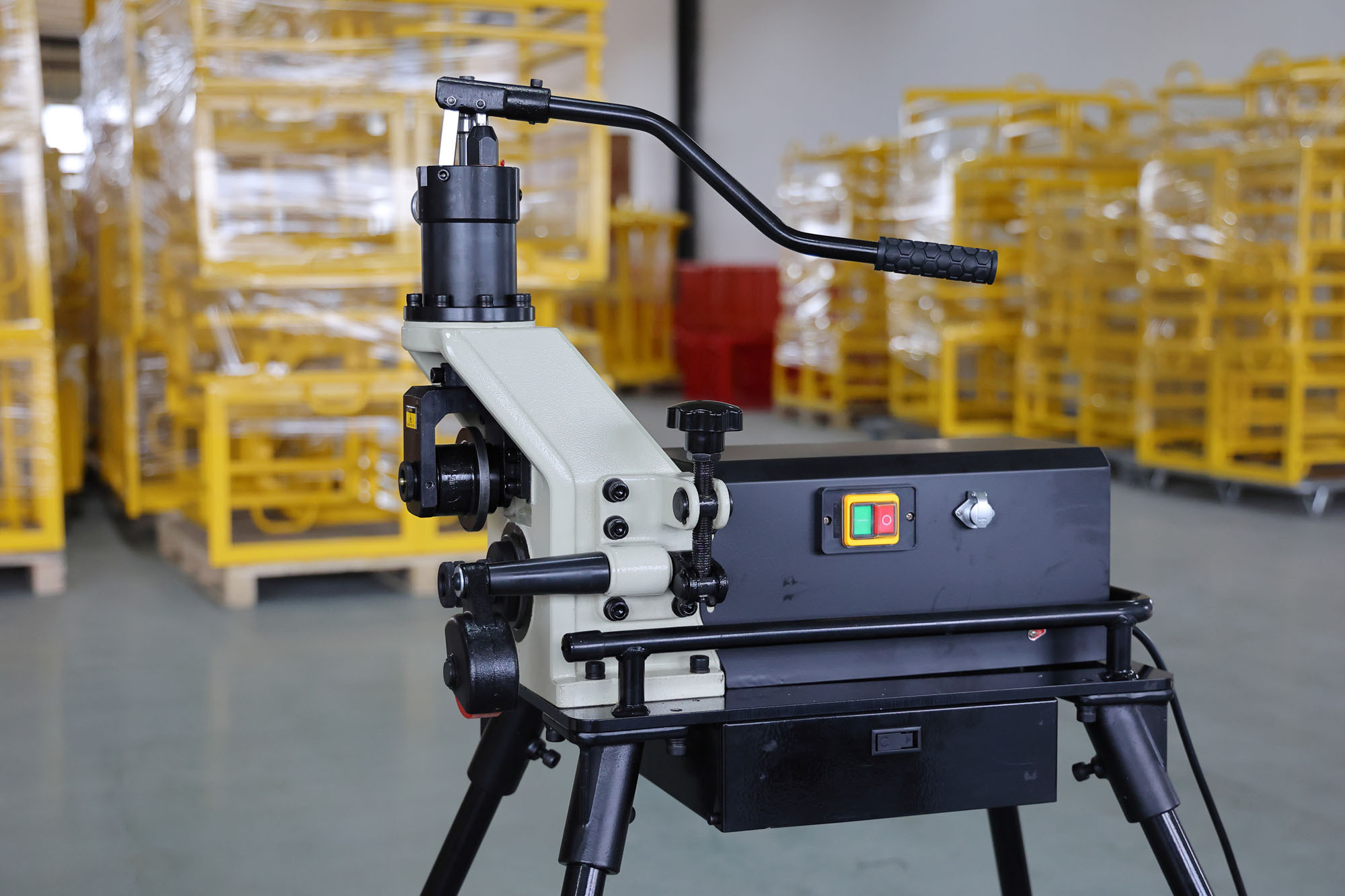
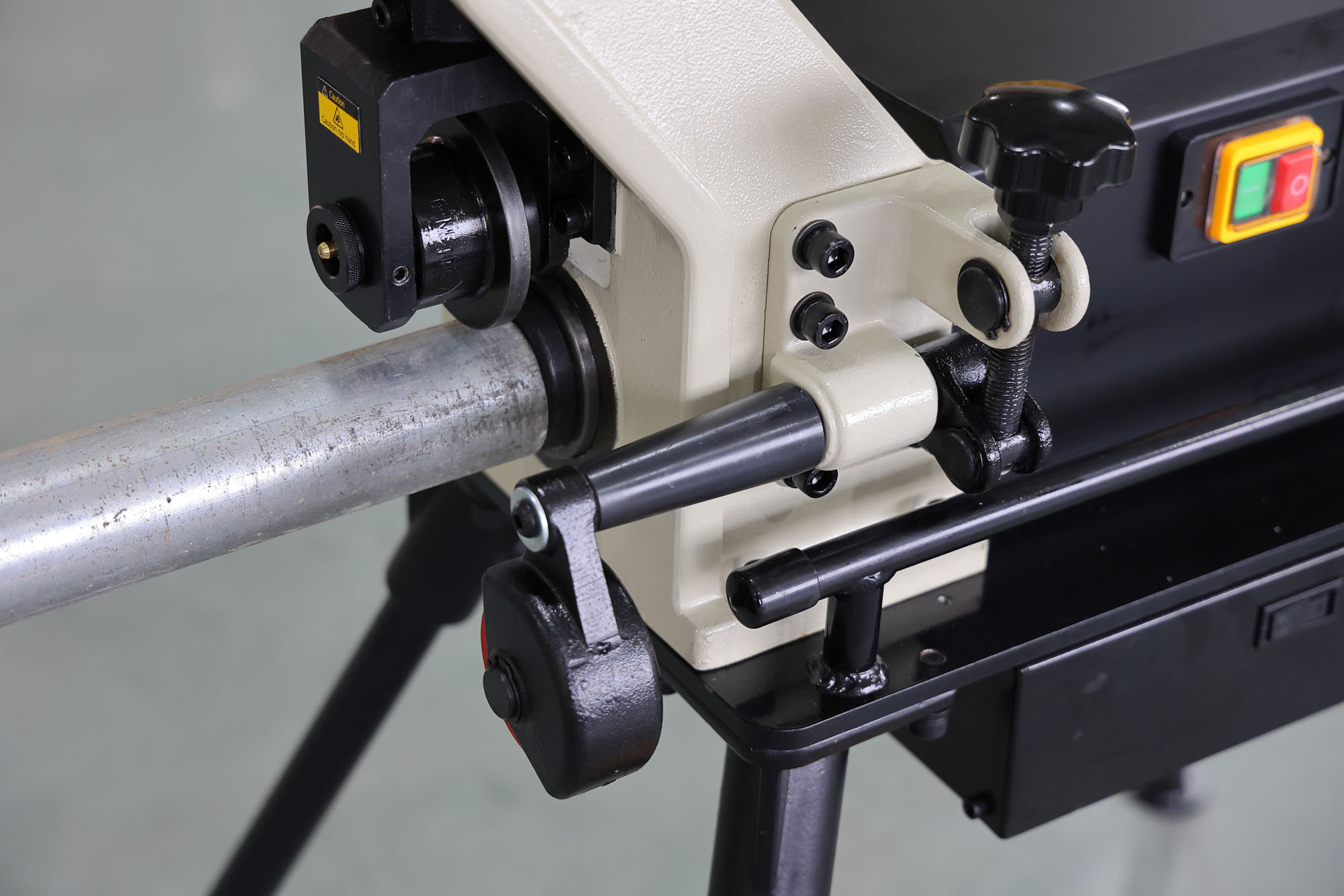
Summaries
The drive roller configuration design of the RG-5X model steel pipe rolling machine is based on comprehensive considerations of speed, efficiency, quality and life. The segmented and refined drive roller configuration ensures the best operating performance within different pipe diameter ranges. This not only improves overall efficiency, but also ensures the accuracy and consistency of rolling grooves, providing users with higher-quality products and a better user experience. This design concept fully reflects our strict requirements for product performance and in-depth understanding of customer needs.